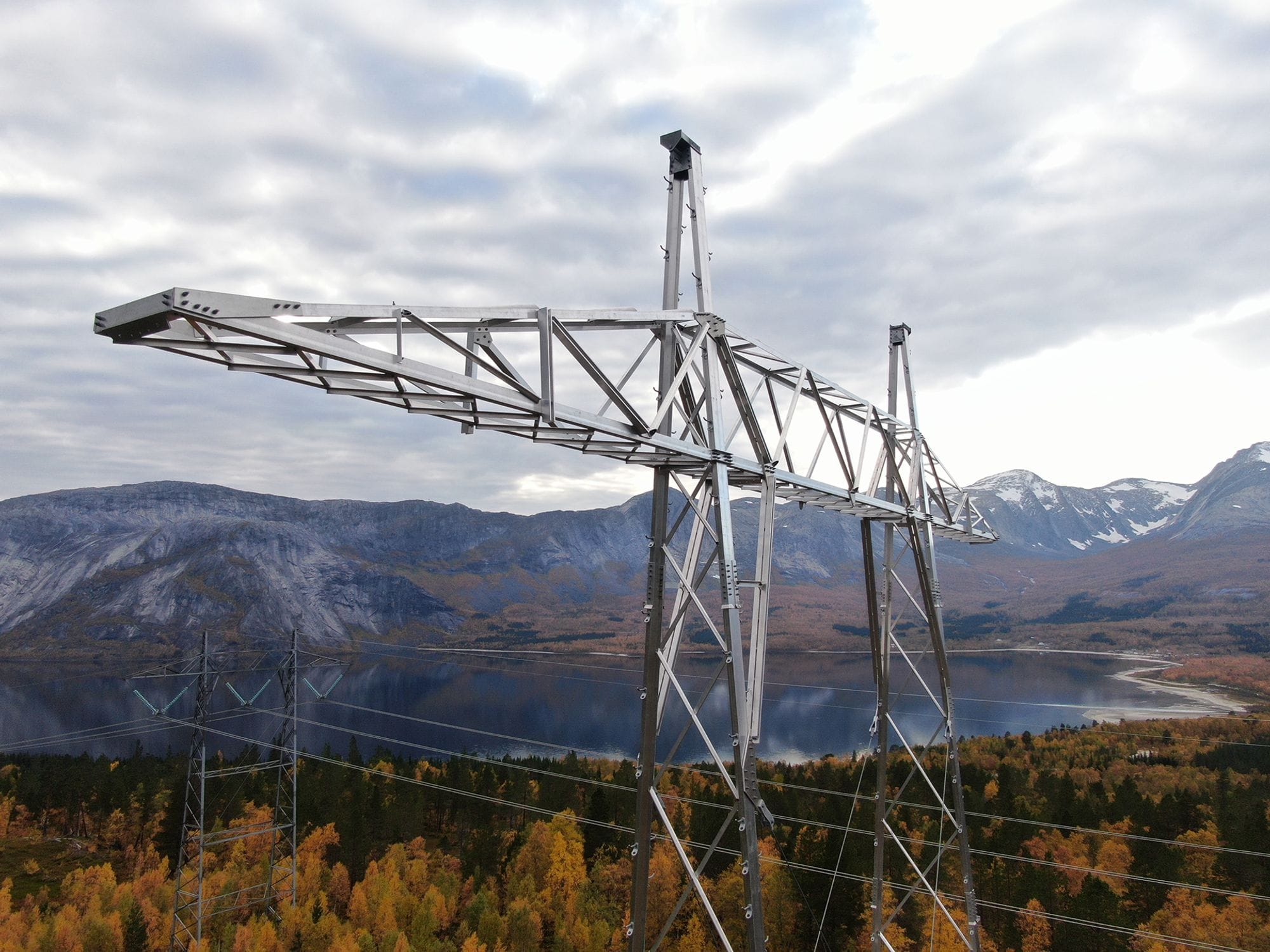
EFLA and Statnett participated in a pioneering research & development project aimed at developing a new tower made entirely of aluminium for the 420 kV transmission network in Norway.
Need for 420 kV transmission network
Statnett powerlines (Norway) are generally constructed in extremely difficult, mountainous terrain exposed to high wind and ice loads. The lack of accessibility to most tower locations requires all equipment, materials and personnel to be flown to the construction site. Reducing the flying time or number of trips has a huge impact on the environment and cost. These constraints and impacts triggered a R&D project aimed at developing a new tower made completely of aluminium for the 420 kV transmission network. EFLA has been involved in the R&D project since its inception in 2015 and has been instrumental in the design of the tower in partnership with Statnett.
The project's objective
- Increase safety through reducing the time that workers need to be on the tower during erection by helicopter. This reduces the risk of an accident
- Lower weight would allow for fewer helicopter flights from the preassembly site to the erection site
- Reduce the erection time and costs, through increasing the amount of the tower section sizes that can be transported in one airlift
- Reduce the CO2 emission, by reducing the number of trips for the helicopter during construction and by the easiness of recycling of aluminium at life end.
The project has been funded by Statnett and the Norwegian Research Council and is a collaboration between diverse industry partners with comprehensive experience from the aluminium industry and research fields.
Tower Development
During the initial stages, the team worked on the development of a prototype tower. A few different tower geometries were analyzed in the preliminary phase such as lattice self-supported towers to internally guyed structures. Determination of a suitable configuration entailed an assessment of:
- Total estimated weight
- Number of elements to assemble
- Mechanical load transfer in elements and connections
- Ease of assembly and construction
- Production cost
- Vibration and fatigue
After the analysis, the internally guyed tower was selected as a feasible option and the most suited alloy type was defined. This included study and selection of the aluminium profile shapes, welded or bolted connections and proper material use.
Reduced production cost
Emphasize was placed on reducing the number of elements and the size of connections (f.ex. quantity of bolts), the impact on aluminium profile shapes, sizes and weight, as well as the potential for vibration issues on slender elements. All these aspects influenced the technical choices.
During this phase, Statnett and EFLA focused on the tower detailing to try and reduce the production cost. This was done by limiting the number of cuts or drilling necessary in the various elements.
Environmental issues
The environmental division of EFLA conducted a Life Cycle Analysis of the carbon footprint of aluminium towers compared to the standard steel towers.
Reduced carbon footprint
The study concluded that over the life cycle of a transmission line (mining for ore and producing the raw materials, design, production, transportation, construction, maintenance, dismantling and recycling), the use of aluminium towers result in a reduction of CO2 emissions by a factor of 2.
Prototype Tower
Following the design and optimisation stage, a prototype was produced by the partners from the Raufoss industry pool. The assembly test went smoothly and highlighted the advantage of making a full-scale model. Minor issues were noticed during this test.
Vibration tests were performed on the full tower, to calibrate with the vibration analysis model. The goal of this analysis was to provide an assessment of the dynamics and self-damping properties of such lightweight structures/elements. In parallel, wind tunnel tests of selected profiles were conducted to assess their susceptibility to vortex-induced vibrations which could result in fatigue failure.
The prototype was then shipped to Sevilla, Spain to be full-scale tested at EUCOMSA. The prototype was successfully tested, reaching an ultimate load of approximately 130% of the design resistance under the critical load case.
Design and erection of a pilot tower
After the success of this first phase, Statnett commenced the second phase in 2018 to develop a pilot tower to install in a line under real operational conditions. EFLA again collaborated on the design of the pilot tower. A few modifications and improvements were applied based on the learnings from the prototype study as well as the vibration testing results. The pilot tower was built close to the new Kobbvatnet substation in Nordland at the start of summer 2019.
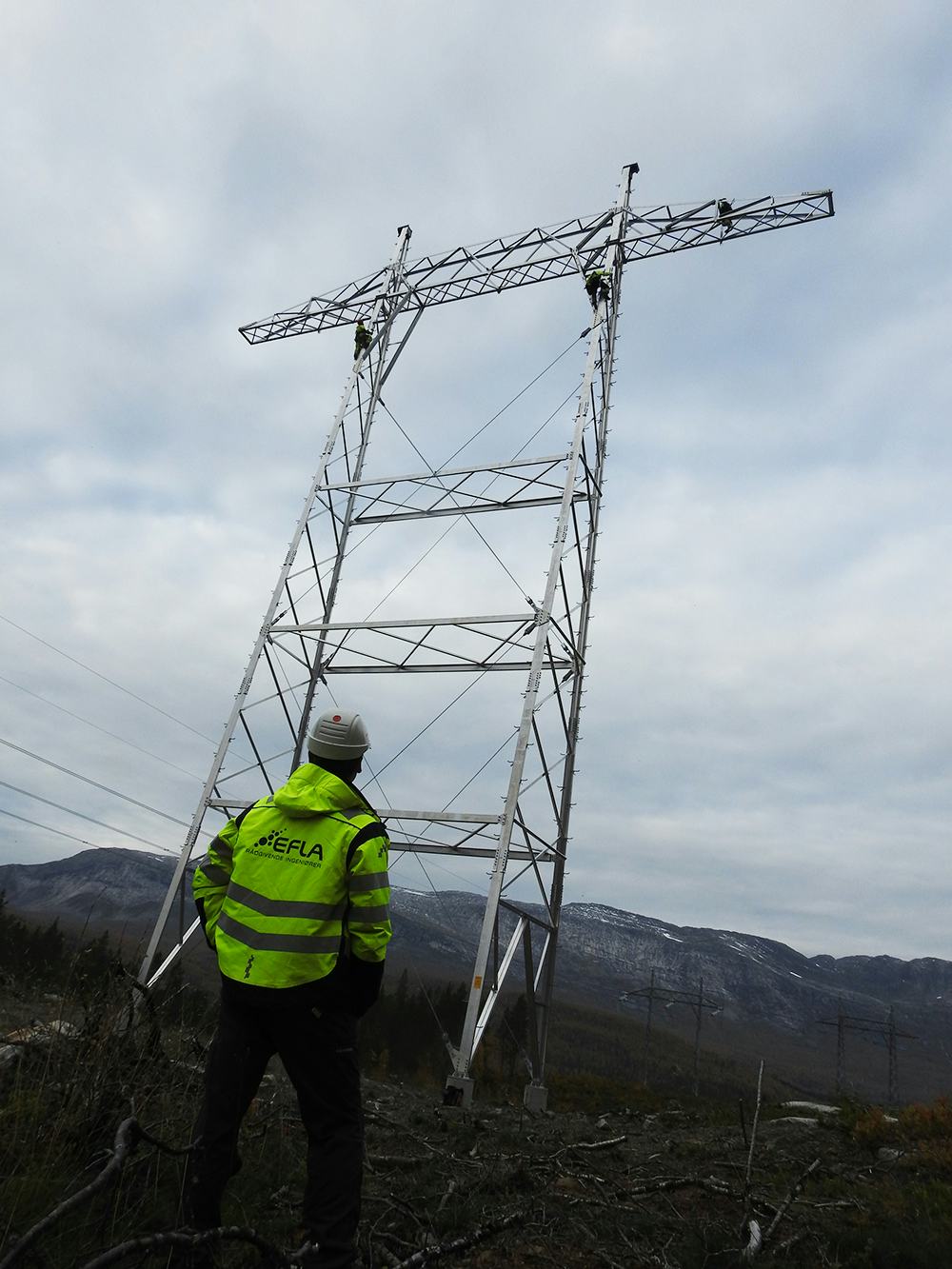
EFLA's staff following the inspection work of the pilot tower. Click for full size.
Tower erection
Statnett received positive feedback from the construction crews regarding erection of the tower. During fall 2020, Statnett and EFLA visited the newly erected tower that has been in position through all 4 seasons. There were no signs indicating possible negative behaviour of the structure or its elements.
The conductors and shield wires were not strung as yet, meaning that the tower is likely standing in a more unfavourable situation with respect to vibration damping. It is thus expected that negative behaviour, if any, with respect to vibration would have already occurred after this time and would have probably been noticeable (loose bolts f.ex.). There were no visible signs of corrosion between the galvanized bolts and the aluminium parts.
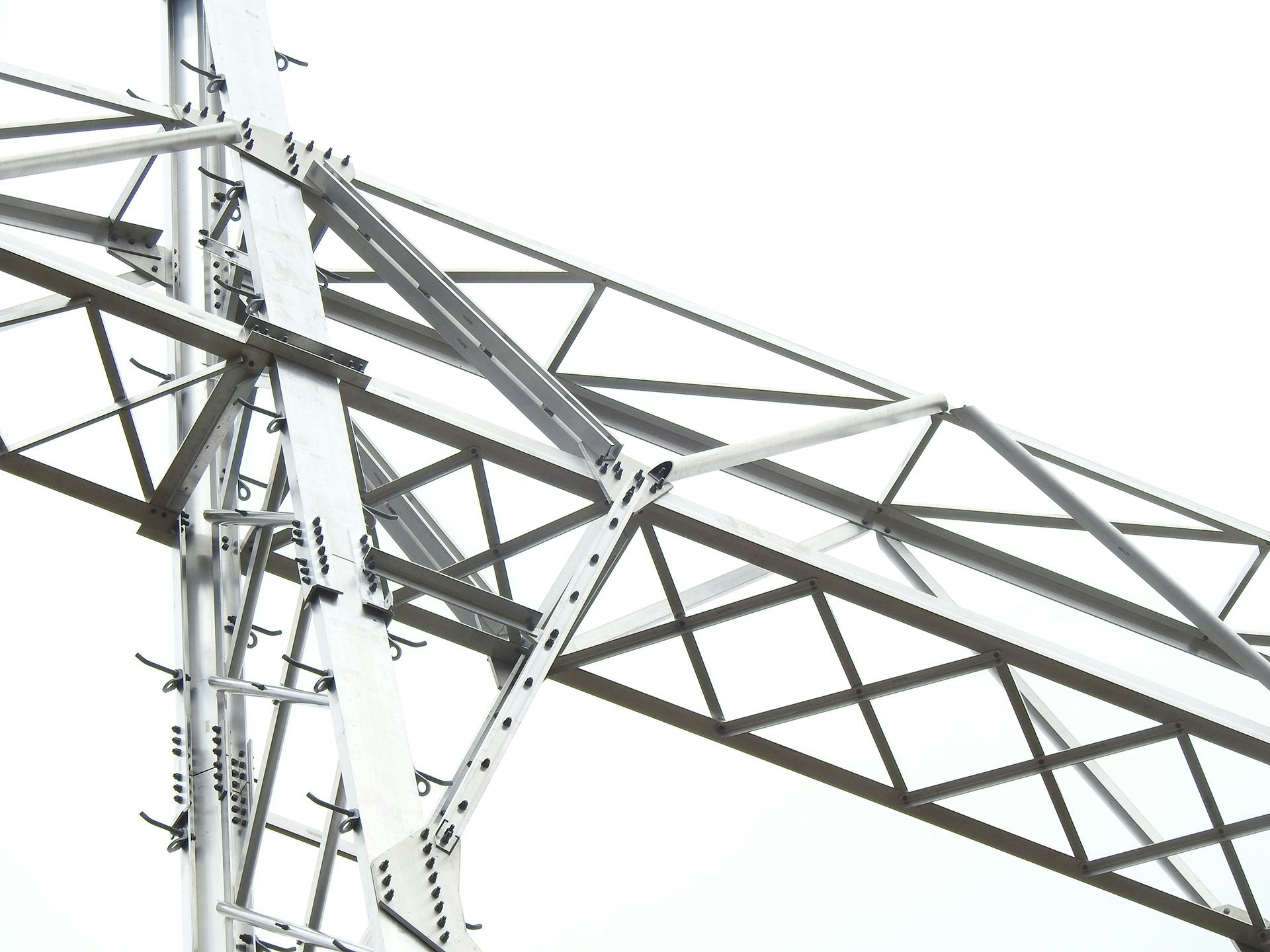
Overview of some of the aluminium profiles.
Further development
During the pilot tower process, EFLA and Statnett worked simultaneously on developing full tower heights range for future use on full transmission lines. Challenges were encountered for the development of profiles for slender unsupported leg elements (typically used for towers with high guy-wire fields in uneven terrain).
The buckling strength of such elements decreases faster in relation to slenderness than that of steel elements. The design of equivalent strength elements in aluminium requires bigger profile shapes.
The restrictions related to extrusion dimensions, as well as weight efficiency and production costs are seemingly setting limitations on the feasibility of such towers in a cost-effective manner compared to steel. With involvement from Norsk Hydro, Statnett has launched a new project to finalize the qualification of the aluminium towers.
The final phase in the process
EFLA was again selected to collaborate on this final development phase. The development is in collaboration with Norsk Hydro and Statnett and includes new solutions for the leg elements, as well as a few other improvements deemed to be more effective for aluminium structures.
The powerful and international team at EFLA, Statnett and Norsk Hydro is hopeful that the development of these towers will go to its term and that aluminium towers will become a reality in transmission lines in Norway.
- 1 / 2
Design arbitrations have led to an internal guyed portal geometry, typical for Statnett.
- 2 / 2
The tower is set in a rough terrain environment.
Contact our experts
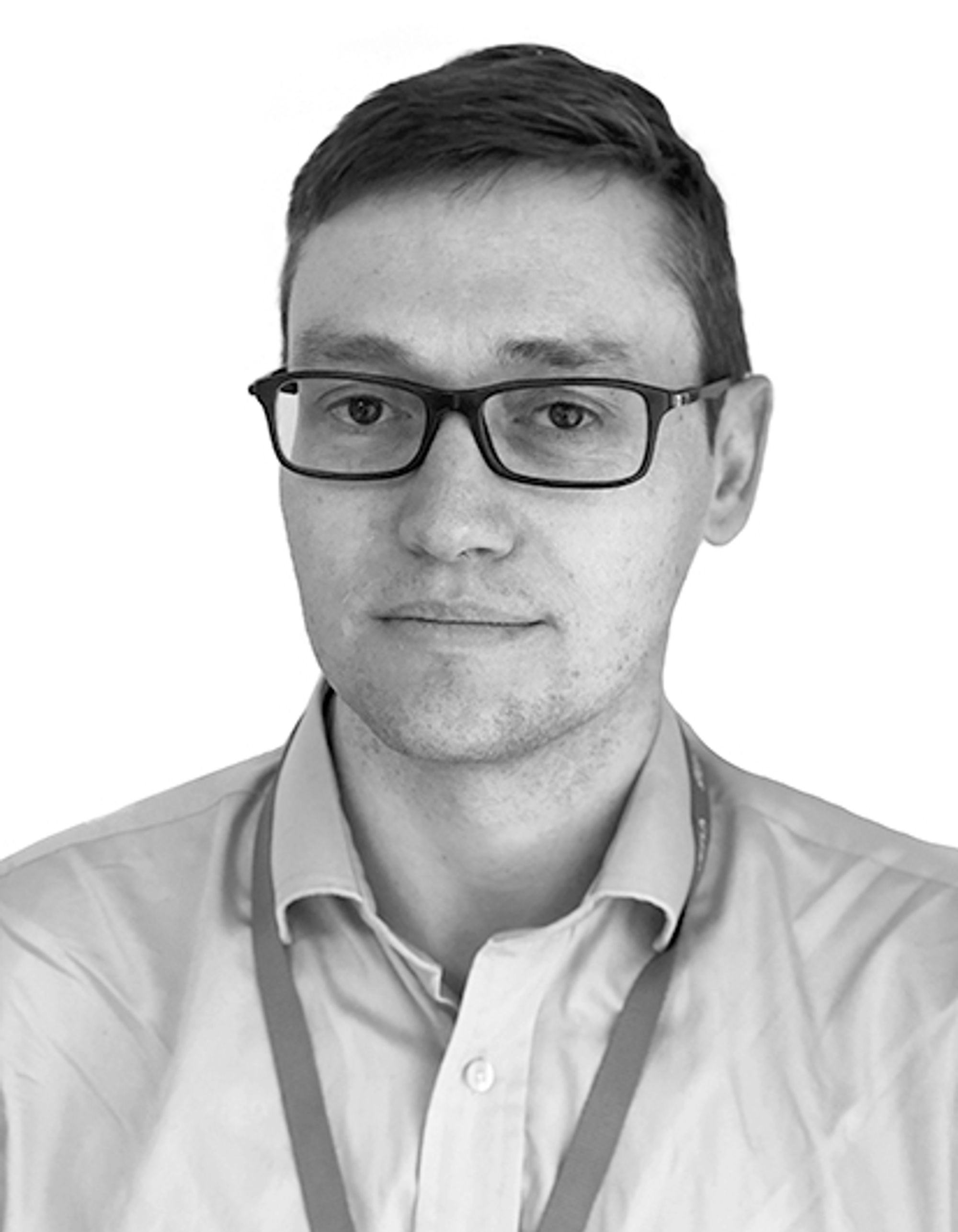
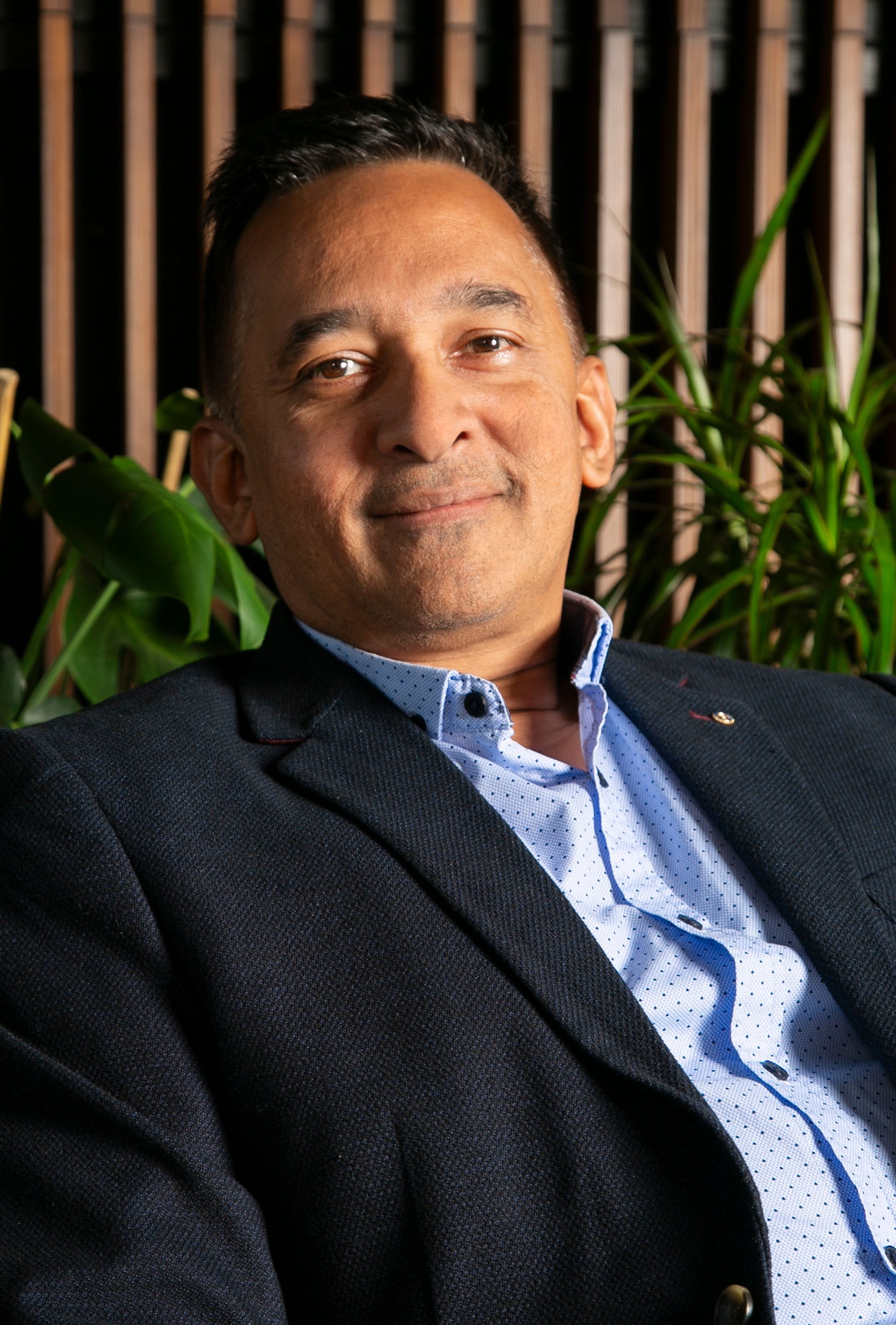