EFLA engineer, Leó Blær Haraldsson, just completed his MSc degree in mechanical engineering. His thesis reports on an interesting project, which has attracted quite a bit of attention. The project examines the possibility of utilizing the thermal energy in exhaust gas from the Alcoa Fjarðaál aluminium plant to heat water for house heating in the nearby community of Reyðarfjörður.
Design of a heat recovery system
Leó's thesis is titled "Viability of a district heating system in Fjarðabyggð using waste heat from Alcoa Fjarðaál" and this thesis covers the basic design of a heat recovery system and distribution system as well as cost estimate.
Aluminium is produced at Alcoa Fjarðaál using a great deal of energy, which comes from an already-built hydroelectric plant. About half of the energy used for aluminium production escapes as heat. Instead of blowing this energy into the atmosphere it could be harnessed for district heating in Reyðarfjörður. According to Leó Blær, „the project findings indicate that heat recovery from the exhaust gases at Fjarðaál is technically possible and will require connecting to only one fourth of the total plant gas flow.“
Reduced fluoride emissions
Positioning of a heat recovery system in an aluminium plant is important. The heat exchanger can be installed in the gas flow before the gas travels through the gas treatment center. At this point, the gas is 15°C warmer than after the gas treatment center and, therefore, there is more heat that can be harnessed. Fluoride binding in the gas treatment center increases with lower gas temperatures which results in less fluoride emitting to the atmosphere. However, the gas is dirtier before it goes through the gas treatment center and can form a dust film inside the heat exchanger pipes. This can increase pressure drops and reduce the heat transfer coefficient. But clever heat exchanger design can minimize dust film formation.
Similar methods in Norway
Leó has studied several successful heat recovery systems in aluminium plants. "For example, in Mosjøen, Norway, there is a heat exchanger connected to the gas exhaust from eight pots and the energy is used to heat the plant itself. This heat exchanger is connected to the gas before it enters the gas treatment center. It has been in use since 2009 and there has been no need to clean it due to dust film buildup."
There are also examples where all the gas from an aluminium plant is sucked through a heat exchanger to cool the gas before treating it in the gas treatment center. The recovered heat is not used for any specific purpose. Rather, this is done instead of blowing cold air or water mist into the gas flow to cool it. This method increases gas volume and calls for more power to the main fans.
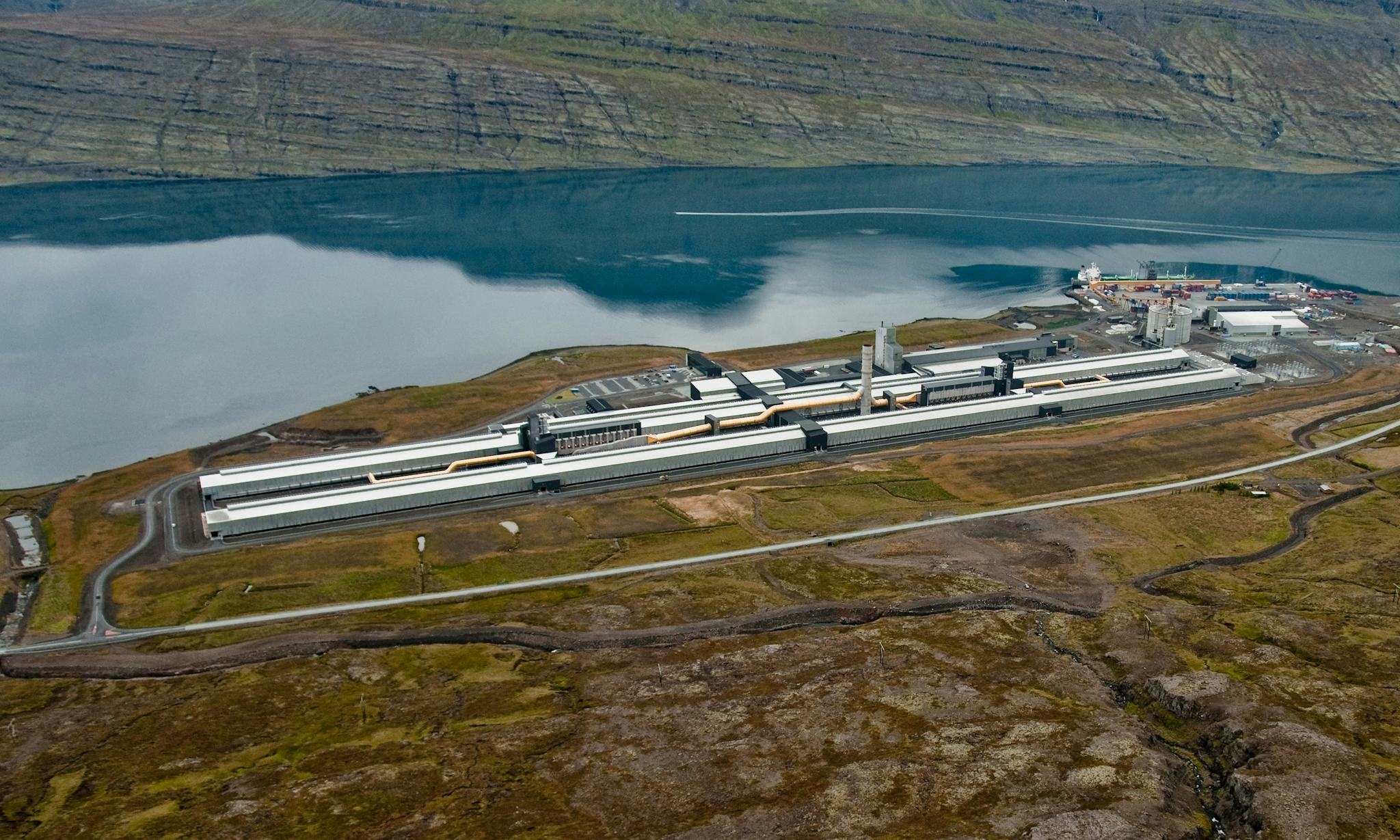
Alcoa Fjarðaál aluminium plant
Excess energy could be used for swimming facilities
Reyðafjörður is in one of the few locations in Iceland where geothermal heat is not available for heating and houses must be heated with electricity. This is considerably more expensive than geothermal heating. The amount of power needed to heat houses and for water for household use in Reyðarfjörður is estimated to be 5 MWth. The heat recovery system designed in this project will supply 5,2 MWth. Thus, there will be excess energy available, particularly during the warmer months of the year. This energy could, for example, be used to heat new swimming facilities in Reyðarfjörður or a warm water beach.
Benefits
The estimated cost for a heat recovery system and distribution system is 2.5 billion ISK. The Icelandic Government currently subsidizes distribution costs for electricity for house heating in Reyðarfjörður and if the Government would provide seed funding amounting to 12 years‘ worth of subsidies no loans would need to be taken. This would be the same amount the Government would be paying in subsidies over 12 years assuming continued heating using electricity. If the project becomes a reality, the Government would no longer need to subsidize distribution costs to Reyðarfjörður and the population would have access to ample hot water at a price similar to what most people in Iceland pay.
Furthermore, Alcoa Fjarðaál can expect social, environmental and even financial benefits from such a project.
Positive reactions to the project
Leó conducted his research in collaboration with EFLA, and Gestur Valgarðsson, who leads the Mechanical division was one of three thesis supervisors. EFLA presented the project on January 23rd at Fjarðaál and the local municipality. The presentation received positive response from both groups and it will be very interesting to follow future steps in this project.
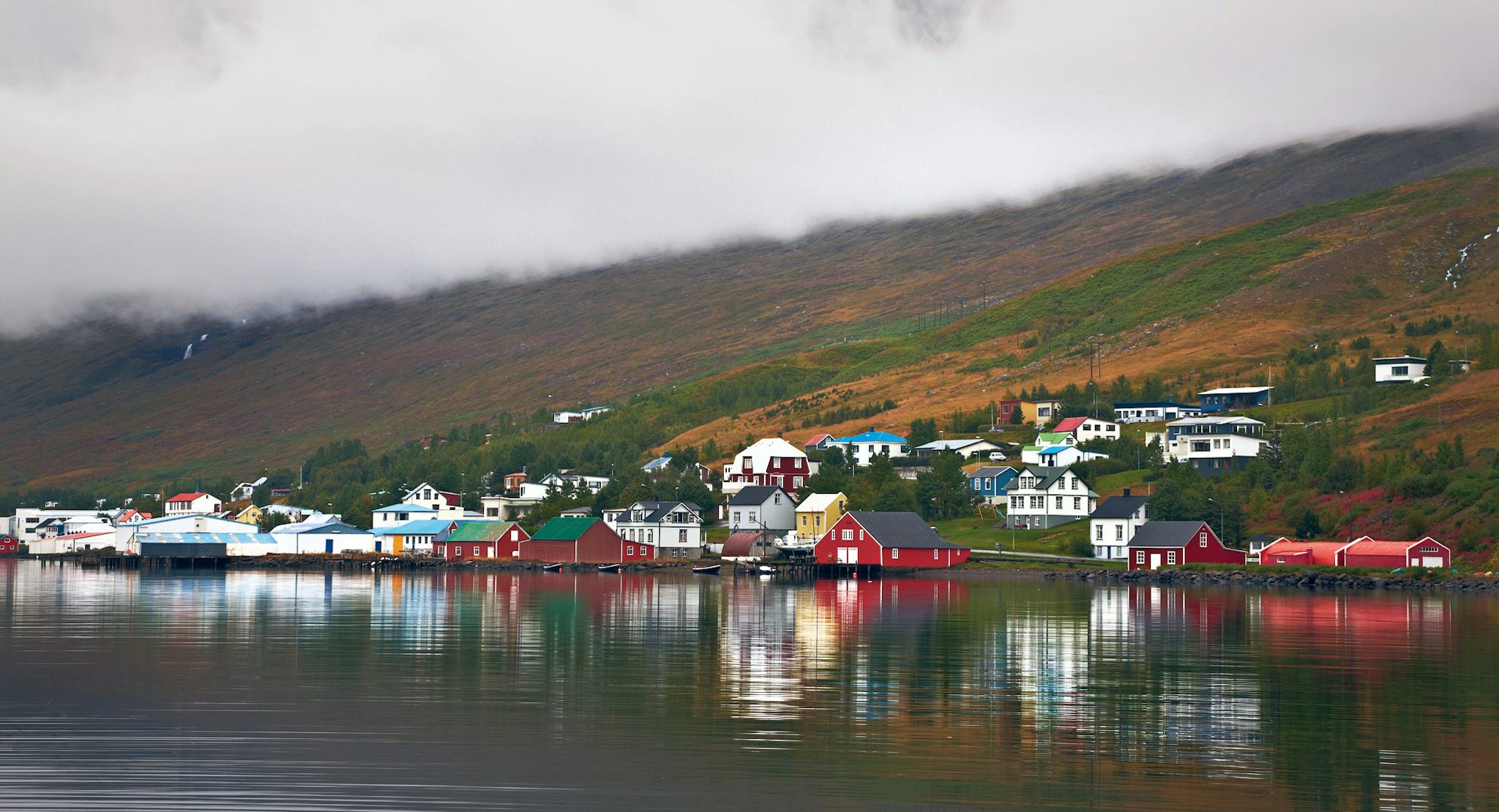
Fjarðabyggð.